Calibration certificates are fundamental in maintaining quality control, compliance, and precision across various industries, including pharmaceuticals, manufacturing, and scientific research. Understanding Calibration Certificates is crucial for anyone using measurement instruments, as these documents validate the accuracy and reliability of your equipment. Let’s dive into what calibration certificates include, why they matter, and how to interpret them effectively.
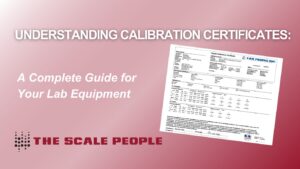
Learn about calibration certificates: key components, environmental factors, measurement data, and how they ensure accuracy and compliance in your industry.
What Is a Calibration Certificate?
A calibration certificate is an official document issued after a measuring instrument has been tested and calibrated against a known standard. It serves as proof that the equipment has been calibrated correctly and that it meets the required specifications. Calibration certificates are vital in various industries where precise measurements are necessary for quality assurance, regulatory compliance, and reliable data collection.
Why Calibration Certificates Are Important
1. Quality Assurance
- Calibration certificates verify that an instrument has been adjusted to meet specific accuracy requirements. This ensures that your measurements are reliable, which is essential for maintaining product quality and consistency.
2. Regulatory Compliance
- Many regulatory bodies, such as the FDA, ISO, BRC, SQF, and GMP, require documented evidence of equipment calibration. A calibration certificate provides this proof, helping businesses meet compliance standards and avoid legal issues or fines.
3. Maintaining Data Integrity
- In fields like pharmaceuticals and research, precise measurements are critical. Calibration certificates guarantee that the instruments used for data collection are accurate, thus supporting the integrity of the data.
4. Extending Equipment Lifespan
- Regular calibration helps detect and correct potential issues early on, reducing wear and tear on your equipment. This proactive approach can extend the lifespan of your instruments, lowering maintenance and replacement costs.
Key Components of a Calibration Certificate
A thorough calibration certificate typically includes several critical pieces of information. Here’s a breakdown of what you should look for:
1. Equipment Information
- Model and Serial Number: Identifies the specific instrument calibrated.
- Manufacturer Details: Provides the contact information of the equipment maker.
- Date of Calibration: The exact date the calibration was performed.
2. Environmental Conditions
- Temperature, Humidity, and Barometric Pressure: These factors are recorded during the calibration process because they can significantly impact the accuracy of measurements. Ensuring these conditions are within acceptable ranges is key to maintaining reliable calibration results.
3. Calibration Standards
- Reference Standards and Traceability: The certificate will list the reference standards used, which are traceable to national or international standards like those from NIST. This traceability guarantees that the calibration aligns with globally recognized measurement systems.
4. Measurement Data
- True Mass vs. Conventional Mass*: The certificate may include both the true mass (measurement in a vacuum) and the conventional mass (adjusted for air density), providing a comprehensive view of the instrument’s accuracy.
- Initial and Final Readings: These show the instrument’s performance before and after calibration, highlighting any adjustments made.
*The True Mass is the mass value assuming it was measured in a vacuum, eliminating any air buoyancy effects. In contrast, the Conventional Mass adjusts this value for air density, making it the practical weight observed in normal conditions. Calibration certificates often report both to provide a comprehensive understanding of the measurements.
5. Uncertainty and Tolerance
- Expanded Uncertainty: This value indicates the possible margin of error, typically calculated to provide a 95% confidence level. It helps users understand the range within which the true measurement lies.
- Maximum Permissible Error (MPE): The MPE section of the certificate shows whether the instrument’s error falls within acceptable limits. If the error exceeds the MPE, it may fail calibration, requiring further adjustment or repair.
6. Technician and Compliance Information
- Technician’s Name and Signature: This confirms the identity of the individual who performed the calibration, ensuring accountability and authenticity.
- Compliance Statement: A declaration confirming that the calibration process followed established procedures and met relevant standards.
7. Calibration Seal
- A unique seal or stamp authenticates the certificate, indicating that it is genuine and verified by the calibration service provider.
How to Interpret a Calibration Certificate
Understanding how to read and use a calibration certificate effectively can help ensure your equipment remains compliant and performs accurately. Here’s a step-by-step guide:
1. Verify Equipment Details
- Start by confirming that the model and serial number on the certificate match the instrument you’re using. This prevents any confusion about the calibration results.
2. Check Environmental Conditions
- Review the recorded temperature, humidity, and pressure. If these factors were outside the acceptable range during calibration, it could affect the accuracy of the measurements.
3. Analyze Calibration Data
- Compare the initial and final readings to see the adjustments made during calibration. This will show you how far off the instrument was before calibration.
4. Review Uncertainty and Compliance
- Ensure the expanded uncertainty is within the acceptable range for your application. Verify the statement of compliance to confirm that the instrument meets industry standards.
5. Assess Traceability
- Check that the calibration standards used are traceable to recognized national or international measurement systems. This ensures that the calibration process was accurate and reliable.
Frequently Asked Questions
Q: Can a calibration certificate be used as legal proof of accuracy?
A: While it’s not legally binding, a calibration certificate is a strong piece of evidence that your equipment meets industry standards.
Q: How often should calibration be performed?
A: The frequency depends on the equipment type and its usage. Manufacturers often provide guidelines, but annual calibration is common for most instruments.
Q: What if my equipment fails calibration?
A: If the instrument does not meet the specified standards, it may require adjustment or repair. Consult our calibration experts to determine the next steps.
Q: Can I calibrate my equipment in-house?
A: While in-house calibration is possible, it requires specialized tools and training. Professional calibration services are recommended for high-precision needs.
Long Story, Short…
Understanding Calibration Certificates is essential for businesses that depend on precise measurements. These documents provide critical details about your instrument’s accuracy, helping ensure compliance with industry standards and maintaining the quality of your operations. By regularly reviewing and interpreting these certificates, you can keep your equipment performing optimally and uphold the highest levels of measurement precision.
If you’re looking to ensure your instruments are calibrated to the highest standards with proper certification, contact The Scale People/Lab People, Inc. for expert calibration services.